New-generation sensor combines lasers and mechanics
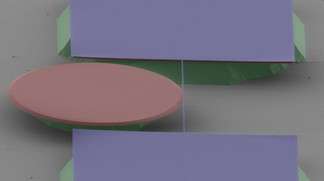
(萌妹社区) -- Swiss scientists have developed a rapid, precise opto-mechanical measurement system that can be embedded into a silicon chip. This new technology could revolutionize the domain of sensors and atomic force microscopy.
Resonators are used to detect infinitesimal quantities of matter in the atmosphere. Here鈥檚 how it works: when a microscopic string comes into contact with a particle or a gas molecule, it vibrates. Each kind of molecule elicits a specific vibration, a bit like a note on a guitar string, giving it a unique signature that can be used to identify the gas or suspended particle in the air, even in minuscule quantities. With colleagues Pierre Verlot and Emanuel Gavartin, EPFL physicist Tobias Kippenberg has made a critical step towards developing more compact, sensitive and precise sensors. The team has published a description of their device, which can be carried on board a single chip, in the journal Nature 萌妹社区.
A disk of light
Researchers are currently in a race to miniaturize resonators. This makes sense, because the smaller the string, the more strongly it will react when it comes in contact with a particle 鈥 in other words, the smaller the sensor, the more sensitive it will be. With a string that鈥檚 only a few hundred nanometers in diameter, the device developed by Gavartin in collaboration with EPFL鈥檚 Center for Micronanotechnology (CMi) is one of the most sensitive that can be operated at room temperature.
The scientists use a laser beam that鈥檚 directed into a tiny glass disk to analyze the string鈥檚 vibrations. The beam circulates 1,000 times in barely 2 nanoseconds, and then exits the disk. The string is placed just above this photon track, and when it vibrates, it perturbs the beam. By comparing the wavelength of the laser when it enters the disk and when it leaves it, the scientists can deduce the movements of the string.
Virtual cooling system
The main obstacle the team faced was a physical phenomenon known as 鈥淏rownian motion.鈥 This causes random vibrations on the string that amplify with every impact and take a certain amount of time to die off. This phenomenon significantly slows down measurements. It鈥檚 a bit like if, after having played a note on a guitar, one had to wait for the string to stop vibrating before the next note could be played.
This difficulty is typically overcome by cooling the system using helium, because Brownian motion is greatly reduced at ultra-cold temperatures. But the EPFL team was able to develop a technique that diminished the Brownian motion and still allowed the system to remain at room temperature. One laser, the 鈥減robe,鈥 detects movements in the string. The signal is processed in real time and used to modulate a second laser, the 鈥渃ontrol,鈥 which is injected into the disk to counteract the effects of the Brownian motion by exerting a counterforce on the string. It鈥檚 a kind of virtual cooling system.
Rapid, precise and simple to use
Using this innovative technique, the scientists were able to reduce the time between measurements 32-fold, while operating at about 20 掳C. This level of precision is extraordinary. 鈥淚f instead of a string, we had a 100m-long bridge, we could, keeping all the same proportions, measure a deformation of a single nanometer, or one ten-thousandth of the diameter of a hair, in real time,鈥 explains Verlot, who was a co-author on the paper.
The system developed at EPFL combines sensitivity 鈥 thanks to the size of the device 鈥 and rapidity 鈥 thanks to the control laser - all without having to resort to a complex and expensive cooling system. Completely integrated into a silicon chip, the system lends itself to numerous possible applications, says Verlot. 鈥Sensors are not the only area in which our system could prove useful. For example, it could also help improve atomic force microscopy systems 鈥 invented in the 1980s by Swiss physicist Christoph Gerber 鈥 and, at a more fundamental level, facilitate the observation and measurement of many phenomena.鈥
Journal information: Nature 萌妹社区
Provided by Ecole Polytechnique Federale de Lausanne